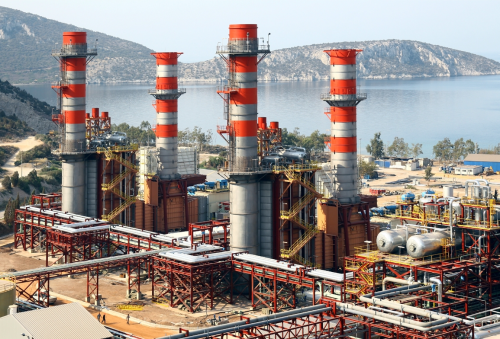
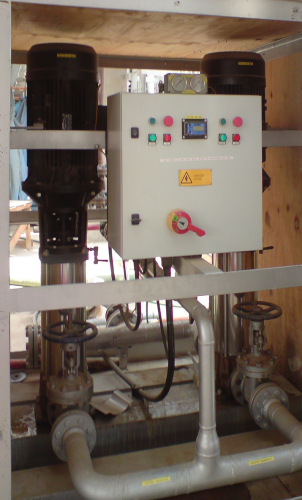
The smallest of dirt particles can do substantial damage to the blades of a steam turbine. For this reason a thorough cleaning of the high pressure steam lines feeding the turbine is imperative before a new installation is commissioned.
This is achieved by blowing and thermally cycling the steam lines with superheated steam which cleans out all the debris left during the construction process. One might expect welding scale, swarf, nuts, bolts and the general detritus left after lines have been welded. In fact, much more substantial solids are frequently flushed out during the cleaning process, including welding rods and, according to Steve Smith, Operations Manager of SABSCO, blocks of wood, tools and even a lump hammer have been encountered.
Steam and Air Blowing Service Co (SABSCO) Ltd is a renowned specialist in the cleaning of steam lines and has provided this service widely throughout the petrochemical and power generation industries especially where steam turbines form an integral part of the process. Cleaning is fastidious to the point where a highly polished mirror-finished ‘target plate’ is positioned within the steam lines and when removed is microscopically inspected for signs of ‘impacts’. A typical specification is no more than 4 impacts, not greater than 0.1 mm, being present on the target plate.
On a recent ethylene plant project in Saudi Arabia (Figure 1), where the ambient temperature is frequently over 45oC, the thermal cycling time was unacceptably long and SABSCO were determined to reduce this dramatically. The solution was to inject 20 tonnes of ambient temperature demineralised water per hour into the steam lines at pressures up to 28 bar to provide accelerated quenching, thus reducing the overall cleaning cycle time. For reliability and redundancy in this hostile environment, this required 2 x 30 kW centrifugal pumps with a 30 m lift, feeding into a single manifold. Simple DOL or star-delta starting was out of the question as a 20 second start-up period was necessary to enable the connecting pipe work to be monitored for minor leakages during start-up and to facilitate a rapid and controlled shut-down if necessary. To enable the necessary degree of control, SABSCO selected two Softstart 58-400-0-S soft-start units which were used to control the two high pressure pumps.
The pump system needed to be built as a portable rig due to the nature of work undertaken. The soft-start units were supplied and built into a control panel also supplied by Softstart UK Ltd which contained additional motor control equipment. Rapid delivery was a must and in the end, the construction of this high pressure pump unit was completed in time for SABSCO to have it delivered to site in Saudi ready for use within a very short time frame. Smith said: “I have used products from Softstart UK on many occasions over the past few years and knew they could deliver. The equipment has proved to be reliable and rugged which is exactly what we need in the environments in which we work. Quality of service from enquiry to after-sales is very high on our list of priorities and we continue to experience this from Softstart. This new and now proven technique has given us and our client clear schedule benefits.”