Can you tell us about the design of the EVO Series process pumps?
Thomas Mapelli: The EVO Series process pump is a real revolution in the process pump world! This pump has been designed to withstand the harshest duty condition and guarantee highest standards availability with the lowest downtime costs. In details, the pump has a three-chamber design, equally spaced and moved by a crankshaft. It provides a smooth flowrate and perfect distribution of forces inside the pump. Every single chamber has been designed with a special patented diaphragm system that has superior flex life and can withstand inlet pressure up to 4 bar. In addition, each chamber includes a secondary leak containment system and leak detection sensors. This guarantees safe operation and Zero contamination in case of diaphragm leakage.
Why are starch-based adhesives increasingly used in the production of paper and cardboard?
Starch glues are likely the most environmentally friendly adhesives; they are generally almost entirely organic, biodegradable and compostable. They are safe for human health and can be applied on packaging in contact with food. For those reasons starch-based adhesives have always been extensively used in paper and cardboard production. The reality is that now with the e-commerce market explosion and environmental concerns, production of ecological paper-based packaging is increasing tremendously and energy consumption in the production process is a first priority.
"The energy consumption of the EVO pump could be up to 9 times better than a standard AODD"
How do the EVO Series pumps handle starch-based glues?
The specific design of the pump allows to combine all the advantages of other positive displacement pump technologies without compromise. The pump is probably the most efficient solution in its range of flowrate and pressure, is robust and reliable, can handle fluids gently without pulsation or shear stresses and is perfect for continuous running. Thanks to its design and layout it guarantees consistent performance at different viscosity ranges. Customers that have tried this pump in starch glue circulation applications are very satisfied. Maintenance intervals are even longer than expected so it makes their Return on Investment (ROI) much better than what has been calculated at the pump order step.
What are the challenges the pump must overcome?
Starch glue circulation is a critical process in cardboard production. Many corrugators run 24/7, this means that starch glue has to continuously circulate. In this situation the main challenges for pumps are Reliability, Availability and Energy consumption. The EVO Series pump answers the call; its special design has been tested over 25,000 hours at maximum load. Pumps installed so far in this application have demonstrated 100% availability over one year of operation. In addition, the new diaphragm design allows much longer intervals between scheduled maintenance compared to an air operated diaphragm pump.
How energy efficient are the EVO Series process pumps?
The EVO Series pump is very efficient! With a global peak efficiency (global = hydraulic + mechanic + electric) of 72%, it is one of the most efficient pumps in its operating range. What I would like to highlight is not just the peak efficiency but also the fact that the entire efficiency curve is very flat. This means that the pump can operate with efficiency above 60% in almost all of the flowrate range, which makes it superior to other technologies, as indicated in the performance graphic below.
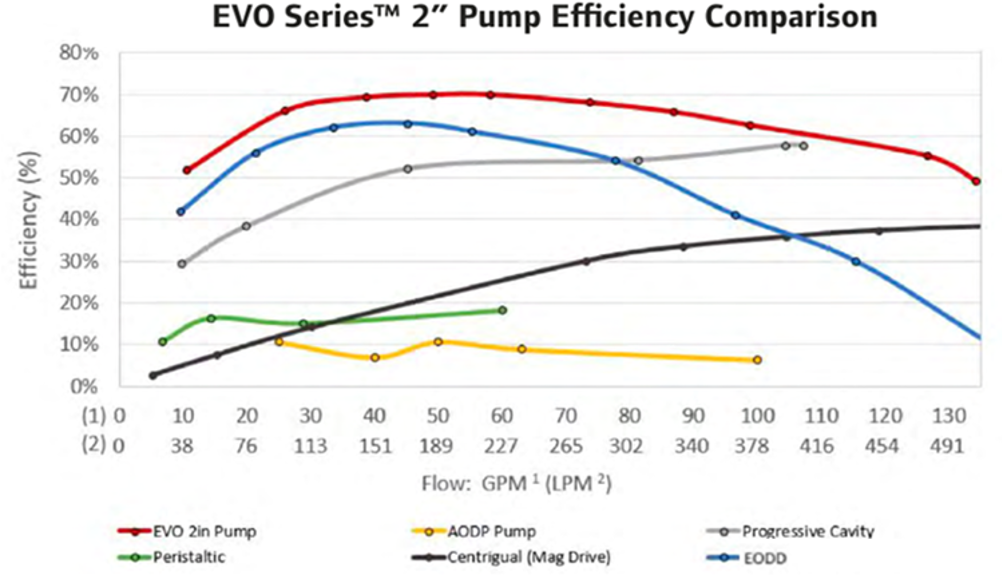
What are the benefits of using the EVO series?
An end user in the paper and cardboard business will experience an incredible energy saving. The energy consumption of the EVO pump could be up to 9 times better than a standard AODD working in the same conditions. Also compared to AODD flow it is much less pulsating, this prevents the usage of any additional pulsation dampener even with complex and long pipe system. The extended maintenance intervals and the fact that the pump can be maintained in place will impact even more positively on customer Total Cost of Ownership. Compared to other electrical technologies this pump does not have mechanical seals and has a unique secondary leak containment system, it eliminates risk of leakage and environmental contamination.
How does the pump reduce energy processing costs?
Compared to other pumps, EVO is extremely efficient. As EVO is electric operated, the pump doesn’t need any compressed air to run those two features to reduce up to 80% the energy costs for the starch circulation process.
What lies ahead for the EVO Series sealless process pumps?
EVO Series process pumps are going to be the core of our future developments. The next step will be the launch of the 1” Polypropylene pump version and advanced IoT connectivity services. After that we do have several additional projects in our pipeline, including new sizes and materials to complement and improve the ARO electric portfolio. The EVO Series is our step into the future of industrial process pumps, stay tuned!
Thomas Mapelli was interviewed for the Pump & Paper feature article in the September/October 2023 issue of World Pumps magazine. To read the full issue click here.