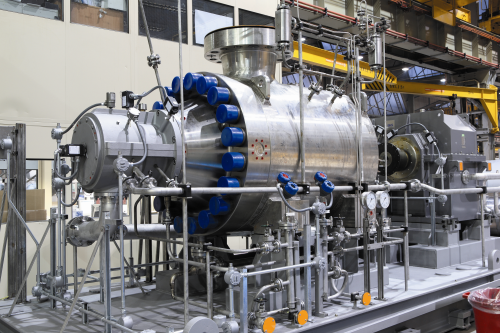
The development of new oil fields in greater depths or in other challenging locations requires dedicated equipment, which has to fulfil demands beyond the performance data of standard pumps. Some pumps, for example, need to meet extremely high head or other critical requirements while at the same time delivering long service life. Seawater injection pumps force water down into the oil well in order to maintain pressure underground, keeping the oil wells productive for a longer time. For the further development of an oil field in the Middle East, Sulzer Pumps designed a tailor-made seawater injection pump to meet the challenging requirements of the customer.
One of the largest oil companies in the world, located in the Middle East, is heavily investing in its oil production. Many different kinds of pumps, including huge seawater injection pumps, are needed in support of this ambitious plan (Figure1). One type of a technically highly challenging injection pump supplied by a competitor of Sulzer did not satisfy the customer. These pumps have many mechanical and hydraulic problems and must therefore be regularly refurbished. As their pump/driver arrangement comprises of five machines in one train, including a booster pump, dismantling is time consuming and difficult. The client was looking for a pump train without a booster pump in order to reduce the number of machines to that found in a conventional arrangement (drive/gear/pump). This condition required a suction stage running at a higher speed than the existing booster pump. Sulzer Pumps had therefore to develop a suction impeller with superior suction performance to satisfy the stringent demands of the client regarding impeller-life.
Largest pump proposed
For a company to be able to react quickly to challenging customer requests means that design concept, tools, and procedures have to be consolidated and cutting-edge experience regarding design and manufacturing has to be available. In this particular case, Sulzer Pumps offered a large 15.6 MW pump with a flow of 4428 m3/h and a head of 1030 m with a guaranteed impeller life of 40,000 hours. With an impeller diameter of 700 mm, the proposed pump is also the largest injection pump designed to date. Based on this offer, the customer awarded Sulzer Pumps with an order for one pump for the new water-injection project and, later on, an order for three to replace the existing pumps. Due to the demanding suction requirements, the biggest challenge was delivering the new suction impeller, including its development, design, and manufacturing.
Fast design tools
Precise and reliable methods to predict the formation of cavitation bubbles in pumps are a must during the hydraulic design of an impeller. Nowadays, all modern computational fluid dynamics (CFD) codes specialized in turbo-machines offer the capability of cavitation-development analysis. Nevertheless, the methods applied in these codes are complete two-phase flow models requiring an unsteady approach. These methods are therefore very time consuming and thus not very well adapted to the design phase of new suction impellers. Hence, Sulzer Pumps uses Neptune, an adapted and much less time consuming Sulzer-owned software for cavitation prediction, which allows the speedy analysis of suction impellers. This approach takes into consideration that the coupling between the main flow and the cavitation development is negligible, which is valid for moderate cavitation development
With the commercial code on a single-processor workstation, the calculation of the bubble formation for one unique flow rate requires about 20 calculation hours. By comparison, calculation for the full operating range (15 flow rates) requires less than 4 hours using Neptune on the same workstation. Even if the prediction obtained from the commercial code appears to be slightly more accurate than the one by Neptune, the information given by the latter code is much more useful to the designer. In particular, Neptune supplies very reliable predictions concerning the NPSH beyond the best efficiency point, an operating state which corresponds to the development of cavitation on the pressure side of the impeller vanes.
Erosion rate predicted
The calculation of the bubble cavity length with Sulzer’s in-house tool also allows the prediction of the associated material erosion rate. The prediction methods developed in the 1980s within the frame of a large research project sponsored by Electric Power Research Institute (EPRI) allow this cavitation-field length to be related to the mean depth of erosion penetration for a given material. It is therefore possible to predict the impeller life for a given suction pressure and a given material on the basis of the numerical calculation of the cavitation characteristics. With these state-of-the-art procedures at hand, the experts at Sulzer Pumps were able to quickly develop the hydraulic design and guarantee impeller life.
Improved inlet flow
The velocity distribution at the impeller inlet influences the operation of the pump. The suction impeller can only perform as predicted if the flow approach to the suction eye(s) is uniform on the circumference in terms of flow velocity and vector. The use of 3D parametric models coupled with modern fluid-flow calculation codes allows the pump manufacturer to adapt these elements to the flow conditions. For this pump, the size and shape of ribs were optimized in numerous iterations (Figure 2). This was particularly challenging because the double-suction impeller requires large flow sections for the return channel to the next stage, which narrowed the flow path to the suction eye.
Flow visualization tests with a model pump especially built for this project were used to validate the design. An acrylic-glass window in the suction casing allowed the observation of bubble formation at the leading edge of the impeller blades. The model tests showed that the design provides extra safety, as the measured bubble cavity length at the available NPSH was well below the critical bubble cavity length (Figure 3).
Proven design procedure
During the tendering phase, the pump concept was checked for the main design parameters, such as pressure, torque, and rotor dynamics, and — in this case — also for manufacturability because of the pump’s huge size. After receipt of the order, Sulzer engineers detailed the design following the Sulzer Pumps design and analysis procedures and standards. The experts investigated critical areas for tightness, maximum stresses, and deformations by means of finite element methods. It was only possible to produce the pump design on time to meet the customer’s schedule, because all design and analysis procedures had been developed and continuously improved over the years based on the company’s vast experience and new developments. This speed was essential to the success of the project. In the final design, stage hydraulics from proven series impellers were installed together with the newly developed suction impeller (Figure 4). A robust balance drum balances the hydraulic axial thrust, and double acting tilting-pad bearings take the residual thrust.
Successful test
The pump was tested with a 15 MW slave motor running at a speed of 2,300 rpm in a closed-loop system (Figure 5). The pump performed excellently, and the predicted flow/head curve and the efficiency were met. The horizontal vibrations of the bearing housing were higher than the vertical ones. This characteristic was attributed to the test-loop set up which allowed the transmission of the flow-induced vibration generated in the huge pressure-breakdown valve. The pump installation in the field is such that even lower vibration can be expected. However, all measured housing vibrations were below the limit on both pump bearing housings (Figure 6). The successful performance test represents a validation of the design and has proved that the design procedures and processes in place are well suited for design and manufacturing of such large and high-energy pumps.
New service center
Sulzer Pumps has supplied many large seawater injection pumps and pipeline pumps to the Middle East. In order to offer local OEM maintenance for such demanding pumps and to show full commitment to its regional clients, the division has expanded its sales offices and will open a service centre in the area during 2008.