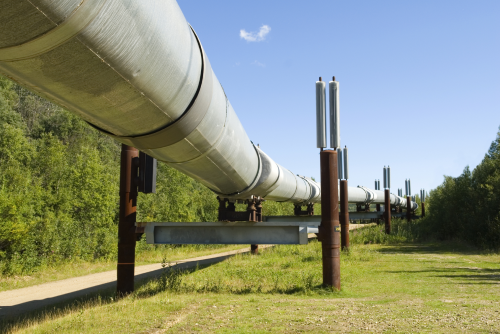
In remote locations where natural gas is extracted from the earth, interstate pipelines facilitate its delivery to refineries, which may be hundreds of miles away. Natural gas pipelines depend on large engines to power stations that compress the gas and continue its transfer down the pipeline. Positioned every 40 to 100 miles along the pipeline, these engines are critical to gas transfer efficiency. Any engine breakdown compromises the integrity of the station and can cause days or even weeks of downtime and significant financial setback.
Keeping these engines properly lubricated is a critical application for diaphragm pumps. Pipeline operators depend on pumps to circulate oil and coolant through the engines to maintain optimal efficiency and prevent downtime. When a compression station is taken offline, pumps prevent the motor from locking up by ensuring that it is properly lubricated. This process is also necessary to pre-lube the motor before a station is put back into operation. However, compression station applications often require pumps to operate in extremely remote areas, creating a number of obstacles to overcome.
Traditionally, operators have struggled to implement pumps at compression stations without a readily available energy source. Pneumatic pumps require the purchase of an air compressor, which must also be electrically powered. Compressed air can be piped to the location, but this is often exceptionally expensive. If a pump fails or is performing poorly, maintenance costs can also skyrocket. Staffing a remote location may not be feasible and it may be days or weeks before a pump can be brought back online. Because air-operated pumps require additional machinery, the risk of damaged or inoperable equipment is increased.
Environmental surroundings also pose a threat to pumps in remote locations. Pumps at compression stations are usually located outdoors or in small enclosures where they are subject to weather conditions. Temperature fluctuations and extreme weather can wreak havoc on performance. If the materials of construction are improperly specified, pumps are subject to corrosion, ultraviolet degradation, stalling and ice-up. Pumps operating around natural gas pipelines can also create a safety hazard when not installed properly, as fluid moving through the pump creates an electrical charge that could ignite a flammable medium like natural gas.
Because of the readily available energy source present in the pipeline, many compression stations now turn to a more convenient option for their fluid transfer needs: natural gas-operated diaphragm pumps. Instead of requiring an air compressor and an additional power source, natural gas-powered diaphragm pumps create a self-contained system by pulling gas from the pipeline and exhausting it back into the compression system. With the advent of international standards to regulate safety and durability, these pumps offer substantial benefits to pipeline operators.
Natural gas-powered pumps
In 2003, the Canadian Standards Association created CSA 2.01, a standard designed to regulate natural gas-powered diaphragm pumps. Among other requirements, the standard recognizes pumps that eliminate static discharge that could potentially cause ambient gas to ignite. The standard stipulates that CSA-certified pumps be provided with a grounding strap to dissipate electrical charges and create safe working conditions.
CSA-certified pumps are tested for performance and durability as well. Achieving certification requires that pumps endure 13,000,000 cycles without failure or leakage. All CSA-certified pumps must complete testing without rupture of the diaphragm or dislocation of any component. In addition, pumps must withstand leak testing at one-and-one-half times the rated pressure. Threaded fittings are also tested against bending and specified torque requirements. The introduction of CSA 2.01 not only established an industry benchmark to measure the quality of natural gas-operated diaphragm pumps, it helped generate significant technological innovations strategic for remote fluid handling at natural gas pipeline applications.
Leak-tight technology
Exhaust discharge is one major difference between air-operated and natural-gas operated pumps. Standard diaphragm pumps come with a muffler that exhausts compressed air to the atmosphere. However, since natural gas cannot be released back to the atmosphere like compressed air, gas-powered pumps require a ported exhaust that is capable of piping the gas away and feeding it back into the compression system. CSA certifications require a higher level of engineering to ensure this gas transfer is completely leak-tight.
Thread sealant on fasteners, an often overlooked leak threat, also helps maintain energy integrity. Utilizing a sealant on fasteners prevents gas bubbles from escaping the motor during operation. Besides obvious safety concerns, gas leaks also create efficiency problems. Pumps that leak gas from the motor yield lower flow rates and require more energy. CSA-certified pumps deliver safety and efficiency to pipeline operators by guaranteeing leak-tight operation.
The CSA certification also requires manufacturers to produce extremely robust, high-tolerance castings and components. To save money, some pump manufacturers do not require their castings to be machined, which produces improper surface finishes and leads to leaking at higher pressures. However, CSA-certified pumps are tested hydrostatically for a burst at five times the rated pressure and monitored for component reaction.
On the major valve housing, high-tolerance, machined bores and valving components create round surface finishes with proper clearances for the valve mechanism. A round surface finish enables O-rings and U-cups to seal as the valve is shifting, creating excellent shift signals and leak-tight integrity at high pressures. CSA certification also encourages manufacturers to utilize an all-metal construction for greater durability, as non-metallic and injection-mold housings are susceptible to UV degradation and tend to be lower tolerance components. On the pipeline, all-metal pumps offer greater reliability to operators.
The CSA standards also require superior wall thickness on pump casings, and high-strength diaphragms. As natural gas causes the diaphragm to expand, pressure in the pump is created by evacuating the fluid chamber. To withstand high-pressure force testing, diaphragm pumps need wall thicknesses between 1/8 in and 3/8 in depending on pump size.
Pump diaphragms should be built with superior flexural strength materials like thermoplastic elastomers (TPEs). The TPEs are more capable of withstanding stress and pressure created by compressed natural gas, leading to longer diaphragm life. Similarly, components that come into contact with the diaphragm must be designed and connected so as not to weaken the diaphragm. Bolted into the connecting rod of the pump between two large washers, the diaphragm is sandwiched in place. Sharp edges on these diaphragm washers or protruding features on the pump casing can wear a thin spot in the diaphragm, causing tearing and rupture over time. To withstand 13,000,000 cycles and a barrage of pressure tests, CSA-certified pumps must be carefully engineered with smooth surfaces.
Best practices & future technology
Pumps should always be operated at the optimal pressure recommended by the manufacturer. Technicians should use a filter regulator to prevent exceeding the manufacturer's specifications. Technicians should also confirm that the pump's material of construction is compatible with the fluid being pumped. In pre- and post-lube applications, pumps utilizing santoprene diaphragms may not be compatible with the oil being pumped. Pipeline operators should install pumps with hytrel diaphragms for optimal performance where lubrication fluids are being pumped.
Inlet pressure is another important issue. In addition to fluid compatibility, operators should make sure that the pressure of the fluid coming into the pump is to specification as well. Proper pump maintenance for natural gas-operated pumps comes down to proper gas pressure, matching pump materials to the fluids being pumped and fluid temperature. Following these guidelines will help to ensure longer pump life.
In the future, remote monitoring technology will continue to develop, decreasing the need to have a maintenance technician on location to monitor equipment. This may be accomplished through the integration of both wired and wireless sensors and system components, so that pump status can be monitored regularly. These sensors might be employed in leak detection through diaphragm failure devices, cycle sensing, pressure regulation and ensuring that the fluid stream is in the proper condition through pressure and flow.