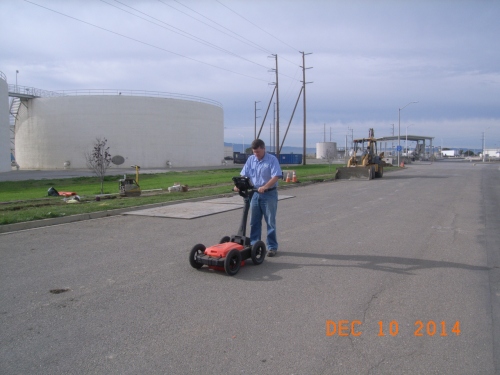
Unfortunately, nine times out of ten, utilities and contractors are faced with the fact that there is no reliable paper record of what has been buried. In some parts of the country, utilities are more than 100 years old, and many utilities have been added or abandoned without being recorded.
Damaging utilities can be costly, leading to cost overruns and project delays. In response, many are adopting subsurface utility engineering (SUE) practices that encourage utility locating. One interesting example is the San José-Santa Clara Regional Wastewater Facility, a large utility in the South San Francisco Bay, which developed a toolbox of methods to identify and document buried utilities. The program has already resulted in huge savings on several major capital improvement projects and brought them in on time and within budget.
An example of the myriad of pipes and utilities (current and abandoned) the utility encountered.
Changing regulations
Most states have quasi-regulatory organisations that serve as a clearinghouse to notify utility owners of upcoming construction projects. These organisations, like Dig Safe in the Northeast or Underground Service Alert in California, then send out someone to identify and stake where utilities are buried. While this service makes it somewhat less likely that a buried utility will be hit, it is by no means fool proof. The information is rarely backed up with adequate records and employees use a very limited amount of technology to locate utilities. So contractors, utility owners, and others responsible for digging are left holding the bag if something goes wrong. If an accident happens the bill can be extremely high, leading to unacceptable project losses.
In addition to project expenses, a few other factors are behind a growing interest in determining where utilities are really buried by using systems – and even more importantly, modes of thinking – that improve utility locating. One is the expansion of gas and oil drilling in the Midwest, where an increase in buried fuel pipelines has led to a greater potential for conflicts.
Another factor is the new PAS (Publicly Available Specification) 128 on underground utility detection, verification and location. The PAS, produced by the UK National Standards Body, BSI, is intended to promote the use and drive the advancement of underground utility records during the planning, design, construction, and operation of underground utility infrastructure. It has resulted in a global interest among engineers and project managers in utilities and concrete to do a better job of locating before digging.
One agency that has decided to respond proactively to these trends is the San José-Santa Clara Regional Wastewater Facility (RWF), located in the South San Francisco Bay. Built in 1956, RWF cleans an average of 110 million gallons of wastewater per day, serving eight cities with 1.4 million residents and 17,000 main sewer connections. The facility is the largest advanced wastewater treatment facility in the western United States. The 2,600 acre site includes a 175 acre wastewater operations area, a 750 acre sludge drying area, and an 850 acre former salt production pond.
Improvements
According to Tim Hayes, Geosystems Manager, knowing what is buried to a high degree of accuracy is absolutely critical to any of the many improvement and repair projects being done on the site. In the past, the utility could depend on veteran staff, those who had worked at the RWF for several decades or more, to tell them “what is buried where” even when there was no written documentation in the files. However, in recent years, many of these veterans have retired and current staff has little or no knowledge of the location of buried utilities.
Furthermore, Hayes explains that the utility did not have a documents management system, with as-built drawings scattered or in huge racks of hundreds of drawings, which makes it difficult and very time consuming to access.
“Given that it is difficult or impossible to pinpoint specific buried utility locations when viewing most of our as-built drawings, and the cost-overruns associated with poorly or undocumented buried utilities, we decided we needed a different approach to managing them. We were convinced such a system would save time, money, and increase safety in the long run,” says Hayes.
However, achieving this goal would take a non-traditional way of thinking – being more concerned with the utility's future needs, rather than the more common “getting your project done and out the door and moving onto the next project” approach.
A look inside the toolbox
In response, RWF implemented subsurface utilities engineering (SUE) practices, establishing its own Subsurface Utilities Management Program. Their goal was to document at least 90% of the utilities on the entire site to avoid problems for their large capital improvement program. They set out to document the utilities both on drawings and in a Geographic Information System (GIS) database.
As part of the new program, RWF adopted the American Society of Civil Engineers (ASCE) ASCE C-I 38-02, Standard Guidelines for the Collection and Depiction of Existing Subsurface Utility Data, which helped them quantify how good the locational/positional accuracy of each of its buried utilities is. The goal of the standards is to “allow the project owner, engineer, and constructor to develop strategies to reduce risk, or at minimum, to allocate risk due to existing subsurface utilities in a defined manner.” Each utility in the GIS is assigned a Quality Level according to ASCE 38-02.
The SUE practices included the implementation of a specific “Buried Utilities Management Toolbox Strategy” for better locating utilities. The toolbox includes a central GIS system; use of multiple utility designating technologies in addition to available drawings; ground penetrating radar (GPR); electromagnetic (EM) locators; magnetic locators; and a laser rangefinder.
The approach is based on the understanding that you cannot depend on any single piece of equipment or data source when you need to locate a buried utility, or a multitude of buried utilities. Each tool or technology has its limitations. Says Hayes, “We found in our situation that the most effective strategy is to use a variety of tools and technologies and develop an approach where they can all work together. The core of our strategy is the GIS, and all buried utilities information is stored in this GIS database.”
Cross checking data
The utility soon learned it could not depend simply on its GPS; verification and cross checking of data with a GPR and the EM locator was necessary, since about 60% of utilities shown on the drawings were either incorrect or not there. This is quite a common situation at many industrial plants, like oil, wastewater or water facilities, where a maintenance group typically installs pipes, which are then buried. A separate capital improvement program deals with engineering design and drawings. The plant maintenance side typically does not document all the many small pipes and conduit installed over many years.
The utility found that GPR was the tool most likely to identify a utility that is not in the GIS. The location and findings of the new information are input directly into the GPS while in the field, and later uploaded to the GIS.
The GIS is dynamic, and is updated daily as the utility identifies additional information about each of its buried utilities. It now contains more accurate buried utilities information than the utility's as-built drawings. “When we go into the field to locate a utility, we upload the GIS data for the area into our GPS, which is connected real-time via cell phone to our GPS Basestation,” explains Hayes. “This allows us to collect data and navigate to any buried utility in our GIS to within four inches.”
In addition, anytime a hole is opened in the ground, and a utility is exposed, they take a photo of it, obtain the location of each utility with the GPS, and upload the information into the GIS back at the office. When they get a USA Ticket and arrive at a location, they usually know what to expect, what is buried where, and what it looks like based on photos. This saves time – and time is money in the construction business.
Two ruggedized GPRs, manufactured by GSSI, are used. Hayes calls the use of GPR a game-changer. “Despite the fact that we are located on the edge of San Francisco Bay Estuary with a high water table and clay soils, our GPR is able to function in approximately 70% of our service area. In some locations we can see anything up to six feet deep, while in other locations we can only see utilities less than one foot deep. Despite these limitations, the use of GPR is absolutely critical to the success of our SUE program.”
The team has been in many situations where their only choice was to use an inductive EM locater, which has a high degree of inaccuracy, or use the GPR. In this situation they typically use GPR because it usually allows them to see what is buried. Without GPR, he says, “We would just be literally throwing our hands in the air and saying we cannot help.”
SUE saves
The SUE program has been successful in reducing construction costs and avoiding construction delays. For example, before the implementation of the Buried Utilities Management Toolbox Strategy, a new headworks facility was constructed at a total cost of about $90 million. RWF had to spend $1 million locating poorly documented or undocumented buried utilities, mostly by potholing at hundreds of locations.
Potholing, actually digging holes to locate utilities, is the most accurate way to identify buried utilities, but is by far the costliest method. On average, a single pothole can cost from $2,000 to $5,000. In addition to the high cost of potholing, the poorly or undocumented buried utilities resulted in a six-month project delay.
Based on a post-project analysis, if the toolbox strategy had been in place for this project, estimated savings would have been approximately $400,000, and there would have been less than three weeks of project delays resulting from poorly documented or undocumented buried utilities.
This project was completed millions of dollars over budget and more than a year late. It was this experience that led directly to the development of the Subsurface Utilities Management Program, of which the Buried Utilities Management Toolbox Strategy is a critical component.
After the implementation of the toolbox strategy, a fire main replacement project was conducted, in which 10,000 feet of new pipeline was installed at a total cost of $1.5 million. About $175,000 was saved by using the toolbox approach to verify buried utilities before construction began. There were less than three days of project delays resulting from poorly documented or undocumented buried utilities, and the project was completed on time and on budget.
Toolbox approach
A final example was a new electrical duct bank installation project, in which 25,000 ft of new duct bank was installed at a total cost of $10 million. Approximately $150,000 was saved by using the toolbox approach to verify buried utilities before construction began, with fewer than five days of project delays resulting from poorly documented or undocumented buried utilities. The project was completed on time and on budget.
As a result of the program success, potholing is now done not to verify buried utility locations, but to verify utility depth and whether there is sufficient underground space to accommodate the new planned buried utility. RWF frequently encounters heavy buried utility congestion (they estimate there are 80 miles of buried utilities located on just 150 acres), so it is critical they have the ability to direct exactly where potholing should be done, what they can expect to find when they pothole, and how many potholes should be done for a project. Before the toolbox strategy was implemented, potholing was conducted based on pure guesswork.
Exact location
Hayes estimates that the utility has documented about 85% of what is buried, including abandoned pipes. They have more than 7,000 geo-tagged digital photos showing exposed buried utilities with their identification and depths. The utility has the ability to use its GPS to navigate to the exact location of each photo and tell what is buried at the location. About 15% of utilities have not yet been documented, primarily the pipes used in the irrigation system for lawns and landscaping, which was installed more than 50 years ago. Originally they focused on other utilities, which if hit would have shut down plant operations – hitting irrigation pipes would just make a mess of the project. After having made such excellent progress with all the other utilities, they are currently in the process of mapping this last system, using GPR along with other tools.
“I have witnessed first-hand what a headache it is for everyone in every way when an undocumented utility or one that was shown incorrectly on the as-built drawings is encountered,” says Hayes. “With the use of GPR and other tools in our toolbox we can accurately identify buried utilities that would conflict with our projects and complete any necessary redesign before construction is started, helping us to complete projects on time and on budget.”